Building a modular solution involves several key steps, from initial planning to final assembly. Here's an overview of the typical process:
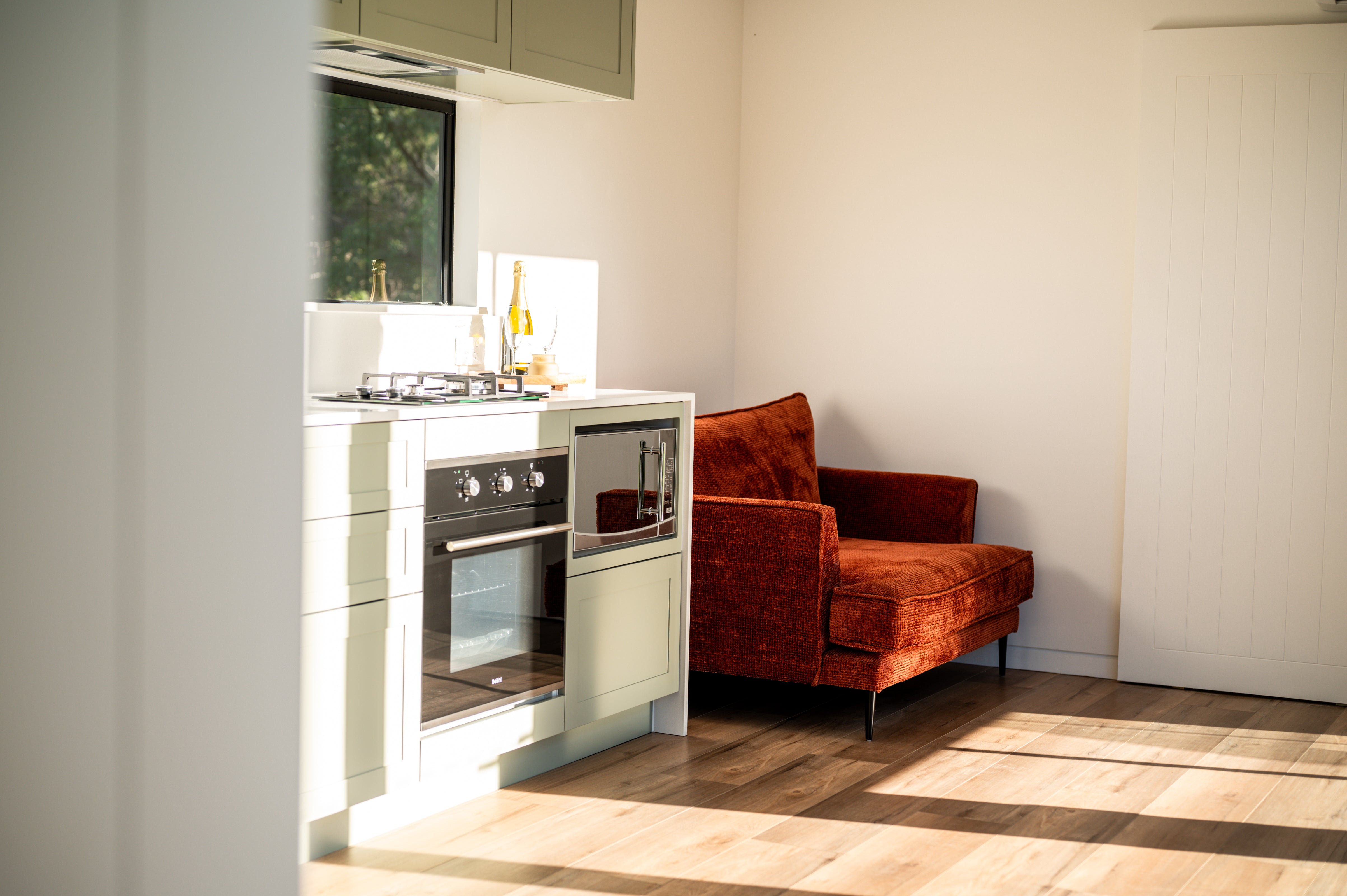
1. Needs Assessment and Planning
- Identify the requirements of the project, including size, layout, features, and budget.
- Conduct a site assessment to determine suitability for modular construction and any site-specific considerations.
- Collaborate with council and engineers to develop a modular design that meets the needs of the project and complies with local building codes and regulations.
2. Design and Engineering
- Develop detailed architectural and engineering drawings for the modular solution, including floor plans, elevations, and structural specifications.
- Incorporate energy-efficient and sustainable design principles to enhance the performance and longevity of our Bayleaf modular solution.
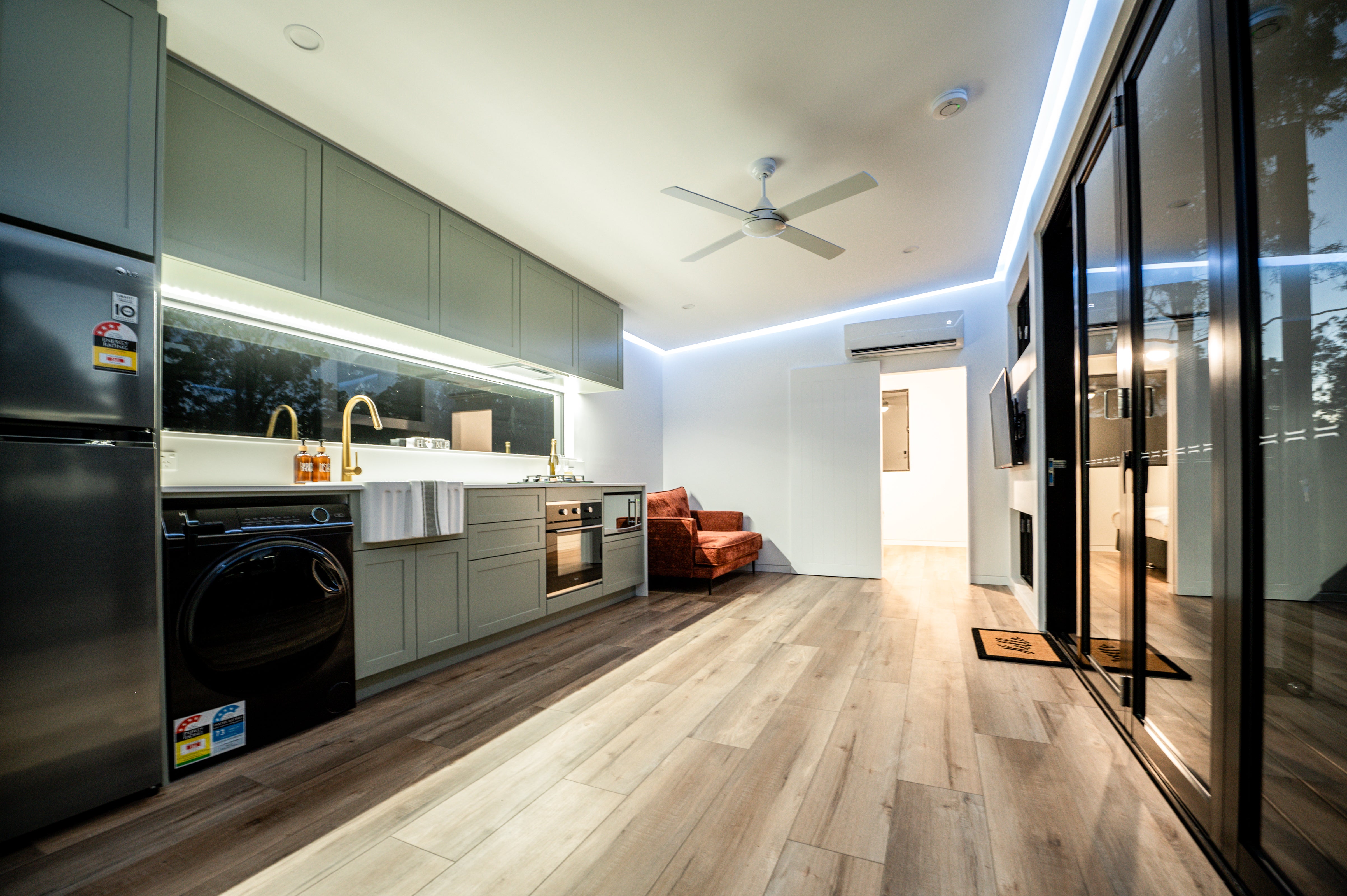
3. Fabrication of Modular Components
- Fabricate the modular components off-site in a controlled environment using advanced manufacturing techniques and precision machinery.
- Construct the individual modules including structural framing, interior finishes, fixtures, and fittings.
- Implement quality control measures to ensure that each module meets the specified design standards and quality criteria.
4. Assembly
- Position and secure the modular components on the foundation according to the predetermined layout and assembly sequence.
- Connect the modules together using structural fasteners, adhesives, and sealing materials to create a cohesive and weather-tight structure.
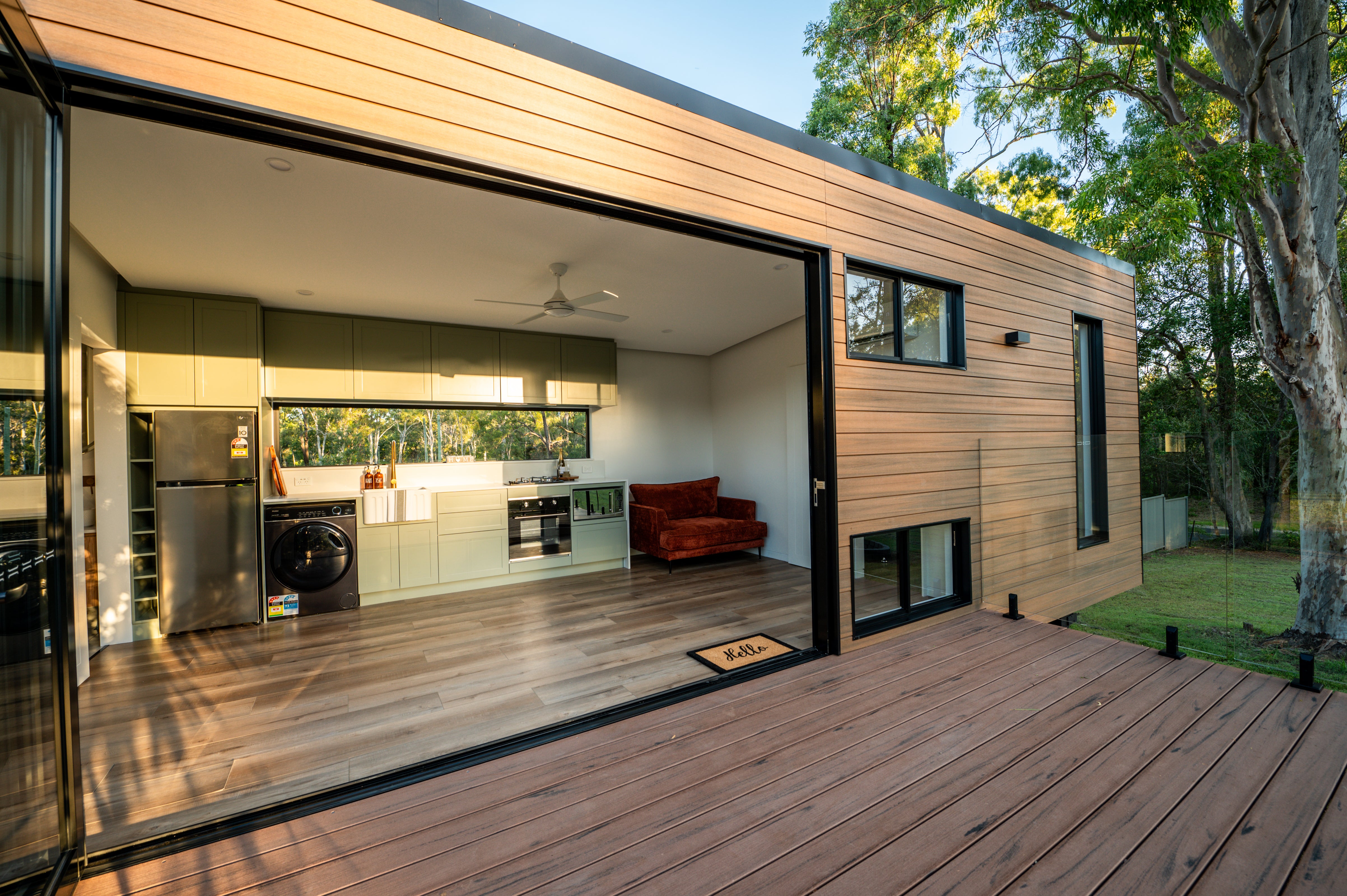
5. Exterior and Interior Finishing and Fit-Out
- Install exterior finishes, roofing, windows, doors, and other components to complete the exterior envelope of the modular solution.
- Complete interior finishes and fit-out work, including drywall installation, flooring, cabinetry, plumbing and electrical connections.
- Customise the interior spaces according to the design specifications and client preferences, incorporating any desired features or upgrades.
6. Transportation and Site Preparation
- Arrange for transportation of the prefabricated modules from the manufacturing facility to the construction site.
- Coordinate with transportation and logistics providers to ensure timely delivery.
- Prepare the site for modular installation, including foundation construction and utility connections.
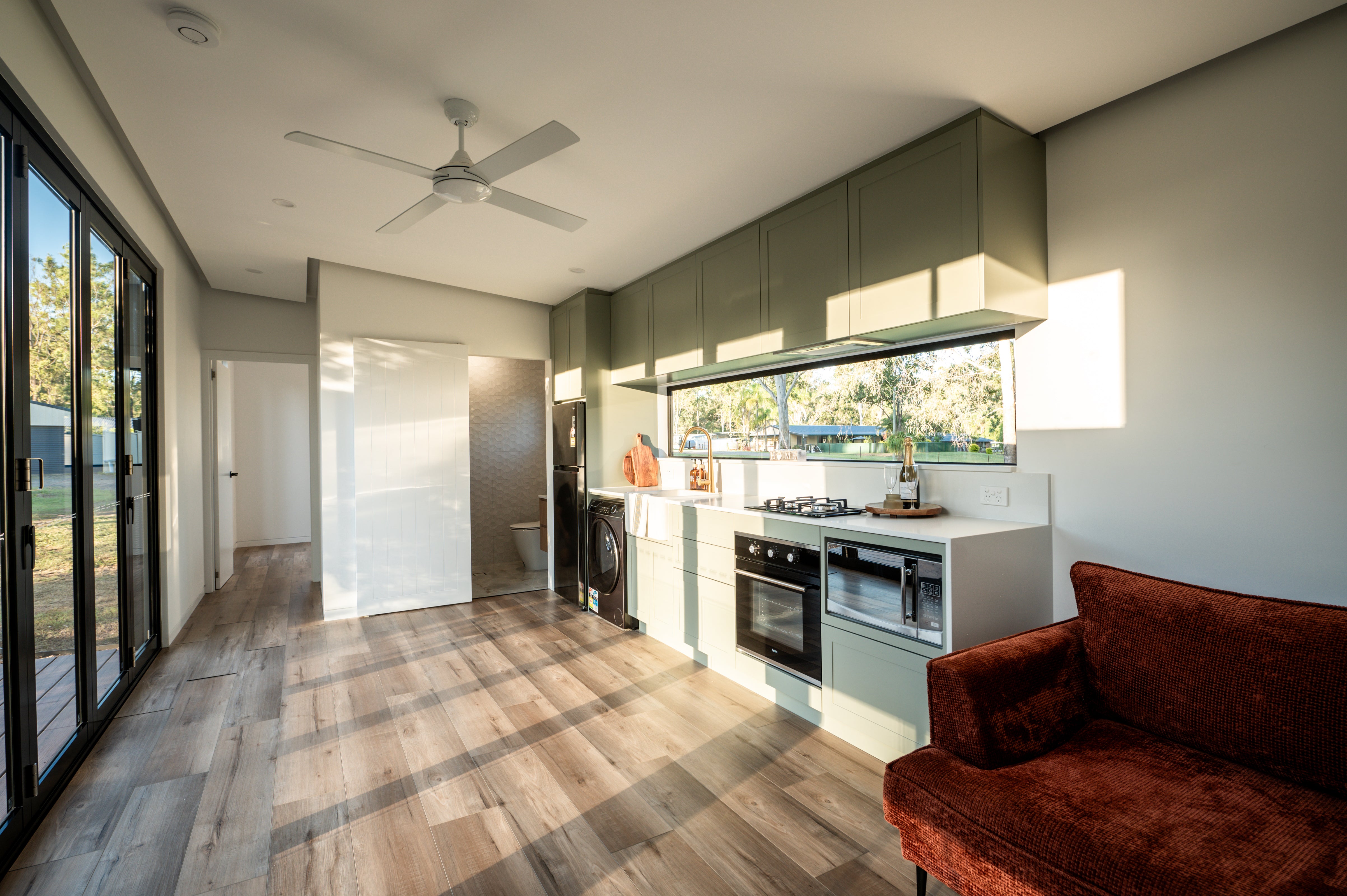
7. Quality Assurance and Testing:
- Conduct thorough quality assurance inspections throughout the construction process to verify compliance with design standards and specifications.
- Perform testing and commissioning of mechanical, electrical, and plumbing systems to ensure functionality, safety, and efficiency.
- Address any issues or deficiencies identified during inspections and testing to ensure the final product meets or exceeds expectations.
8. Handover and Occupancy:
- Conduct a final inspection and walkthrough of the modular solution with the client to ensure satisfaction and address any remaining concerns.
- Obtain necessary approvals and certifications from regulatory authorities to confirm compliance with building codes and regulations.
- Hand over the completed modular solution to the client and provide training or support as needed for occupancy and ongoing maintenance.